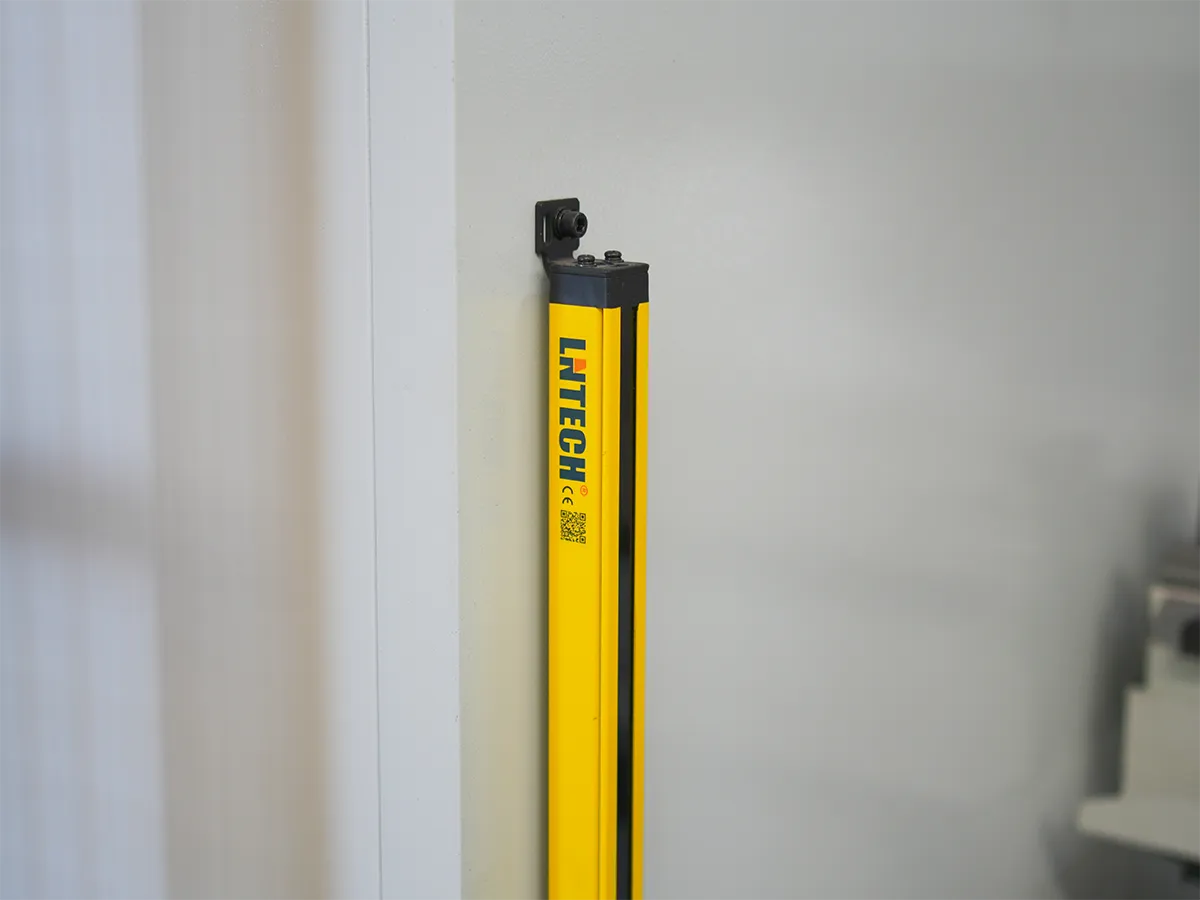
Imagine the precision of bending metal sheets into perfect shapes with the press of a button. This is the magic of a press brake, a powerful tool in the world of metalworking. But mastering its operation, ensuring safety, and maintaining its performance are critical to achieving flawless results and preventing costly errors. Whether you’re a seasoned technician or a newcomer to the manufacturing industry, understanding the ins and outs of press brake usage is essential. What are the key steps to operate this machine safely? How can you maintain its hydraulic system for optimal performance? Dive in to uncover expert tips and detailed guidance that will elevate your metal bending skills and keep your press brake in top shape. Ready to become a press brake pro? Let’s get started.
Before using a press brake, it’s important to perform several checks to ensure safety and proper functioning.
Conduct a thorough visual inspection of the press brake, including the electrical system, motor, and grounding. Verify the oil level in the hydraulic system. Then, choose the appropriate upper and lower molds based on the product’s shape, thickness, and size. Fasten the upper die to the fixing plate and adjust the lower mold to match.
Ensure the back gauge is correctly set to match the desired bending angle on both upper and lower die sets.
Once the pre-operation checks are complete, follow these steps to operate the press brake:
Start the machine using foot pedals or control panel commands. This allows the punch to press down on the metal sheet to initiate the bending process.
Properly position the metal sheet onto the press brake, aligning it with the chosen die set and ensuring secure placement.
Jog the foot switch to adjust the stroke of the upper die. Ensure the distance between the upper and lower molds is set correctly relative to the sheet thickness. Fine-tune the stroke to ensure the upper mold moves down to the required position and then retracts.
Activate the press brake gently, applying pressure slowly and gradually to start the bending process. Make necessary adjustments during the process to achieve the desired bend.
Adhering to safety protocols is essential during press brake operation.
Never place hands, arms, or any part of the body in the point of operation (the area between the dies) even when the press brake is stopped. Be aware of hazards such as nip points, rotating parts, flying chips, and sparks.
Always use safety devices like guards and emergency stop buttons. Wear proper PPE, such as gloves and safety glasses, to protect yourself from potential hazards.
Regular maintenance is crucial for the longevity and efficiency of a press brake.
Regularly inspect and maintain all mechanical components to prevent malfunctions. This includes checking the hydraulic system, oil levels, and electrical components.
Provide comprehensive training on machine safety protocols, including understanding machine hazards, familiarity with safety features, and emergency stop procedures.
Keep the work area free of obstructions to avoid tripping hazards and ensure smooth operation.
After completing the bending process, switch to manual mode and lower the ram to align the dies. Turn off the main motor and inspect the finished product for quality.
Safety during press brake operations is essential to prevent accidents and ensure a safe workplace. Proper safety protocols protect operators and ensure efficient machine operation.
Operators need thorough training on the press brake’s operation, components, safety features, and emergency procedures. They should be familiar with the location and use of the STOP button and know how to shut off the main power panel in case of emergencies or when changing dies.
Operators should wear tight-fitting clothing and rolled-up sleeves to avoid entanglement with moving parts. They should also avoid loose items like neckties, watches, and jewelry. Using personal protective equipment (PPE) such as safety glasses and gloves is crucial to protect against flying debris and other hazards.
By adhering to these safety protocols and best practices, operators can significantly reduce the risk of accidents and ensure the safe and efficient operation of press brakes.
The frame acts as the backbone of the press brake, providing essential stability and precision during the bending process. Constructed from welded steel plates, the frame forms a rigid structure that supports all other components, ensuring minimal deflection under load and maintaining bend accuracy and consistency.
Central to the press brake’s operation, the bed holds the metal sheet stationary while the ram moves vertically to apply force. The ram is driven by a hydraulic system, which may include hydraulic cylinders, gear pumps, piston pumps, or vane pumps, depending on the specific application. The precise movement of the ram is crucial for achieving accurate bends.
Punches and dies are essential tools used to form bends in the metal sheet. They come in various shapes and sizes, typically made from hardened steel or tungsten carbide. The selection of punches and dies depends on factors such as the type and thickness of the material, the desired bend radius and angle, and the press brake’s specifications. Proper selection and maintenance of these tools are vital for achieving high-quality bends.
The back gauge system ensures accurate positioning of the metal sheet for repeatable, precise bends. It moves along the X-axis using linear guide rails and ball screws for precise adjustments. The back gauge system can be manually adjusted or controlled via a CNC system, allowing for automated positioning and increased efficiency in production.
The control system of a press brake can be manual, NC (numerical control), or CNC (computer numerical control). CNC systems are the most advanced, allowing operators to program bending parameters such as angle, length, and tool settings. This automation enhances precision, reduces setup times, and minimizes errors. The control system is integral to the overall functionality and efficiency of the press brake.
Safety devices protect operators from hazards and include features like light curtains, safety guards, hydraulic clamps, presence sensors, pullbacks, and restraints. Light curtains detect the presence of an operator and stop the machine if necessary, while mechanical guards and clamps prevent accidental contact with moving parts. Ensuring that these safety features are functional and properly used is essential for safe press brake operation.
Understanding these components and their functions is fundamental to operating a press brake efficiently and safely. Each part plays a vital role in the bending process, contributing to the machine’s overall performance and the quality of the final product.
Air bending is a common technique where the punch partially presses the material, not fully touching the die. This method offers greater flexibility in achieving various bend angles and reduces tool wear. However, it requires precise control to account for springback, a phenomenon where the material partially returns to its original shape after bending.
In bottoming, the punch presses the material into the die until it fully conforms to the die’s shape. This method provides higher accuracy and consistency in the bend angle but requires more force compared to air bending. It can only produce angles that match the die’s shape, limiting flexibility.
Coining involves compressing the material between the punch and die, creating a permanent deformation. This technique offers the highest accuracy and repeatability but demands significant force and precise tooling. Coining is especially beneficial for reducing springback in materials prone to this issue.
CNC bending machines utilize computer-controlled movements to manipulate the material with exceptional precision. These machines can execute complex bending operations consistently, making them ideal for high-volume production runs. CNC technology enhances efficiency by reducing setup times and minimizing errors.
Laser measuring systems use lasers to measure the angle and curvature of the bend in real-time, allowing for immediate adjustments if deviations are detected. This significantly reduces the margin of error and improves the overall quality of the final product. This technology is crucial for achieving high precision in metal bending.
Simulation software allows operators to predict how the material will behave under stress before any actual bending occurs. This helps identify potential issues such as springback or material deformation, reducing waste and improving efficiency. By simulating the bending process, operators can optimize parameters and achieve better results.
Accumulated dust, debris, and metal shavings can cause wear and tear on the machine. Regular cleaning helps prevent these contaminants from affecting the machine’s performance, ensuring smooth and accurate operations.
Regular inspection and lubrication of moving parts, such as the ram, back gauge, and hydraulic cylinders, are crucial. Proper lubrication reduces friction, minimizes wear, and ensures smooth and precise movements, contributing to the longevity and accuracy of the press brake.
Over time, the machine’s components can become misaligned, leading to inaccurate bends. Regular calibration ensures that the press brake’s settings are accurate and consistent, maintaining the precision of the bending operations.
Using safeguards like presence sensing devices, pullbacks, and restraints is crucial to keep workers away from hazardous areas during operation. These safeguards must be securely in place, tamper-resistant, and durable for normal use to ensure operator safety.
Proper training is paramount before operating a press brake. Operators should understand the machine’s controls, safety features, and emergency procedures, including the use of the STOP button and securing stock before engaging the ram. Comprehensive training reduces the risk of accidents and enhances operational efficiency.
Operators should wear tight-fitting clothing, avoid loose items like neckties or jewelry, and ensure that shirt sleeves are rolled up to prevent entanglement with moving parts. Appropriate personal protective equipment (PPE), such as safety glasses and gloves, is essential for protecting against potential hazards.
Operators should be familiar with emergency procedures, including shutting off the main power panel before changing dies and notifying a supervisor immediately if there is a jam during the operating cycle. Clear understanding and adherence to emergency protocols can prevent serious injuries and machine damage.
Conducting a daily visual inspection of the press brake to check for any loose or damaged parts, leaks, or abnormal noises is essential. Promptly addressing any issues helps prevent them from escalating into more significant problems, ensuring continuous and safe operation.
Step bending is useful for large bend radii or thick materials. This involves making incremental bends along the length of the material, reducing the force required and improving control over the bend angle. Step bending is particularly useful for achieving smooth and consistent bends in challenging applications.
Regular inspection and maintenance of the tooling are critical to preserving the quality of bends. Dull or damaged tools can lead to defects in the workpiece and reduce the lifespan of the press brake. Ensuring that the tools are in good condition enhances the overall performance and accuracy of the bending process.
Regular maintenance is essential to ensure the longevity and optimal performance of a press brake.
Maintaining the hydraulic system is crucial for the press brake’s performance and efficiency.
By following these maintenance and troubleshooting tips, operators can ensure the efficient and safe operation of their press brakes, minimizing downtime and extending the equipment’s lifespan.
Below are answers to some frequently asked questions:
To operate a press brake, start by inspecting the equipment and installing the appropriate upper and lower molds. Adjust the backgauge according to job requirements and set the stroke controller for the correct position. Perform a trial bend with scrap material to ensure proper functioning. Activate the machine using foot pedals or control panel commands, ensuring accurate metal sheet bending. Follow safety protocols, including operator protection, use of safeguards, and wearing PPE. Regularly inspect and maintain the machine to ensure optimal performance.
To ensure safety while using a press brake, operators must be thoroughly trained and familiar with the machine’s operation and safety protocols. Use safeguards such as mechanical guards, light curtains, and two-hand controls to keep hands away from danger zones. Wear appropriate personal protective equipment like gloves and goggles, and avoid loose clothing. Maintain a clean and organized work area, conduct regular inspections, and follow proper maintenance schedules. Implement lockout/tagout procedures before maintenance, and ensure emergency stop buttons are accessible. Adhering to these practices can significantly reduce the risk of injuries.
The key components of a press brake include the frame, which provides structural stability; the ram, which moves vertically to bend the metal; the bed, where the metal sheet is placed; the punch and die, which are the tools used for bending; the backgauge, which ensures accurate positioning of the metal; the hydraulic system, which powers the machine; the electrical system, which controls operations; the transmission system, which transmits power; the tool clamping system, which secures the tools; the control system, which manages machine functions; and the safety system, which protects operators from hazards.
To maintain the hydraulic system of a press brake, regularly check and maintain the hydraulic fluid levels, ensuring they are within the recommended range and change the fluid at specified intervals. Monitor the system oil temperature to keep it between 35°C and 60°C, replace or clean hydraulic filters with each oil change, and inspect for leaks in hoses, seals, and connections. Clean hydraulic components monthly without detergents, keep the reservoir clean, and conduct daily and weekly inspections for any issues, as discussed earlier. Following these steps ensures optimal performance, safety, and longevity of the hydraulic system.
Advanced techniques for precision bending using a press brake include air bending, bottoming, and coining. CNC bending machines enhance precision through computer-controlled movements, while laser measuring systems ensure accuracy by measuring bends in real-time. Simulation software helps predict material behavior, reducing waste. Material selection, considering factors like tensile strength and ductility, is crucial, as is thorough operator training. Step bending is useful for large radii or thick materials. Regular maintenance and adherence to safety protocols are essential for optimal performance and safety, ensuring high precision and efficiency in bending operations.
To troubleshoot common issues with a press brake, start with regular maintenance, including daily visual inspections and following the manufacturer’s manual for schedules and guidelines. For hydraulic problems, check for leaks, maintain fluid levels, and ensure the pump and valves are functional. Inspect and clean electrical components, addressing any loose connections or faults. Lubricate parts as recommended to reduce wear. Address specific issues like abnormal noise by checking connections and replacing worn parts, and resolve weak bending force by examining valves. Ensure operators are trained and follow safety protocols to prevent accidents and prolong machine life.