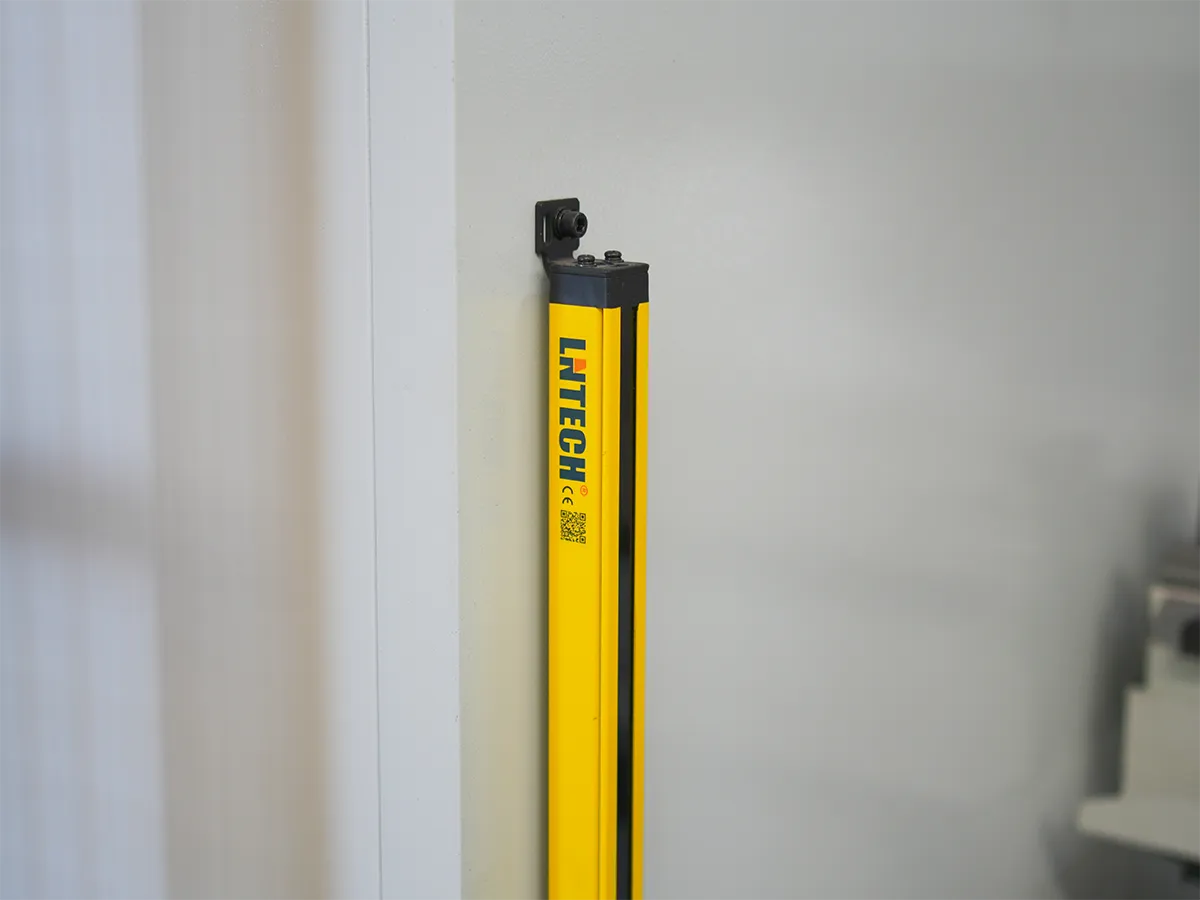
Are you looking to master the art of press brake operation and ensure peak efficiency in metal fabrication? Whether you’re a seasoned professional seeking to refine your skills or a beginner eager to dive into the world of press brake machinery, comprehensive training is essential. This guide will walk you through everything you need to know, from selecting the best training programs to understanding critical safety protocols and acquiring necessary certifications. Discover the key operational skills and troubleshooting techniques that will elevate your expertise. Ready to become a proficient press brake operator and enhance your career prospects? Let’s get started!
A press brake is an essential tool in metalworking, designed to bend sheet metal into different shapes. The operation of a press brake involves several critical components and processes to achieve precise and accurate bends.
There are several types of press brakes, each with unique features and advantages suited to different applications.
Mechanical press brakes, powered by a flywheel and electric motor, are fast and efficient but offer less control and flexibility.
Hydraulic press brakes utilize hydraulic cylinders to move the ram. They offer greater control and force, making them suitable for bending thicker and tougher materials. These machines can perform more complex bends with higher precision.
Pneumatic press brakes use compressed air to power the ram. They are typically used for lighter-duty applications and offer faster cycling times compared to hydraulic press brakes. However, they may not provide the same level of force and precision.
Servo-electric press brakes use electric motors to drive the ram. These machines are highly precise and energy-efficient, offering excellent control over the bending process. They are ideal for applications requiring high accuracy and repeatability.
Press brakes are vital in industries like automotive (for making brackets and frames), aerospace (for crafting precise components), construction (for forming structural elements), and appliance manufacturing (for producing panels and enclosures). These machines are essential for producing parts that contribute to the assembly of complex products and structures.
To become proficient in operating a press brake, specialized training is essential. A comprehensive training program should cover various aspects, including fundamental principles, safety protocols, and advanced techniques. Here are key elements to consider when choosing a press brake operator training program:
A robust training program should encompass the following topics:
Training programs can be delivered in various formats to cater to different learning preferences and needs:
Apprenticeships provide a blend of on-the-job training and classroom instruction. This approach allows aspiring press brake operators to gain practical experience while learning theoretical aspects. Apprenticeships typically involve:
Technical colleges offer specialized programs in metal fabrication and machine operation, including press brake operation. These programs often include:
Vocational schools focus on providing practical skills and technical knowledge needed for specific trades. Programs for press brake operators at vocational schools typically include:
By considering these options and evaluating the content, format, and support provided by each training program, aspiring press brake operators can choose the right path to develop their skills and advance their careers in metal fabrication.
Press brake operators must possess a solid understanding of the mechanical aspects of the machinery they work with, including knowledge of the machine’s structure, working principles, and critical components such as the punch, die, ram, and back gauge. Operators should be able to perform basic mechanical repairs, make necessary adjustments, and troubleshoot minor mechanical issues to ensure smooth operation and minimize downtime.
Accurate bending operations require press brake operators to have strong mathematical and measuring skills. Operators need to interpret blueprints, perform basic trigonometry, and understand tolerances to achieve precise bends. They need to use tools like calipers, micrometers, and protractors to check bend accuracy and ensure the final product meets specifications.
Safety is paramount in press brake operations, and operators must be well-versed in safety regulations and protocols, including the use of personal protective equipment (PPE) such as gloves, safety glasses, and steel-toed boots. They should be familiar with safety devices like safety interlocks, light curtains, and emergency stop buttons. Conducting pre-operation checks, maintaining a clean work area, and following strict safety guidelines are essential practices to minimize risks and prevent accidents.
Operators of modern press brakes, especially those with CNC controls, need to be proficient in computer use. They should be capable of setting parameters, programming the machine, and using software to control the bending process. This includes understanding both manual and graphical programming, as well as being able to troubleshoot and optimize CNC programs for efficient and accurate production.
The ability to read and interpret blueprints is crucial for press brake operators. Blueprints provide detailed specifications and instructions for the parts to be produced. Operators must understand symbols, dimensions, and notes on blueprints to accurately set up the press brake and perform bending operations. This skill ensures that the final product adheres to design requirements and quality standards.
Press brake operators need physical stamina and strength to perform their duties effectively. The job often involves standing for long periods, handling heavy sheet metal, and performing repetitive tasks. Good eyesight and manual dexterity are crucial for handling small objects, making precise adjustments, and using hand tools.
Effective communication and teamwork are vital in a manufacturing environment. Press brake operators must be able to convey information accurately and timely to supervisors, engineers, and other team members. This ensures that production processes run smoothly, issues are addressed promptly, and quality standards are maintained. Collaboration with other team members is essential for achieving common goals and meeting production targets.
Strong problem-solving skills are essential for press brake operators to identify and resolve issues quickly. This includes troubleshooting hydraulic and electrical systems, addressing hydraulic leaks, and inspecting electrical connections for faults. Operators must be able to think critically, make informed decisions, and implement effective solutions to maintain continuous production and minimize disruptions.
Hands-on training is crucial for developing practical skills and gaining experience with press brake operations. This includes supervised practice sessions, demonstrations, and the use of various training formats such as virtual classroom training, on-demand video training, and in-person training. Certification programs from reputable organizations, like the Fabricators & Manufacturers Association (FMA), validate operators’ skills and enhance their credibility in the industry.
Press brake operators are responsible for ensuring the quality of the finished parts. They must use measuring tools to inspect each part and verify that it meets quality standards. Regular maintenance tasks, such as daily cleaning and inspection, monitoring hydraulic fluid levels, and checking for loose bolts and electrical faults, are essential to keep the press brake in optimal working condition and prevent breakdowns.
Certifications for press brake operators validate their skills and knowledge, ensuring they meet industry standards and are proficient in handling the machinery. Earning certifications can enhance an operator’s credibility and improve job prospects.
The Crane Institute Certification (CIC) offers a highly valued Forklift Safety and Inspector Certification. This certification exceeds OSHA’s training requirements and demonstrates an operator’s commitment to safety and operational competence.
The American Welding Society (AWS) provides the Certified Welding Engineer (CWEng) certification, which is beneficial for press brake operators involved in welding operations. This certification validates expertise in directing welding processes, complementing metal fabrication skills.
The Construction and Demolition Suppliers Association (CSDA) offers an Operator Certification program. This six-day training focuses on safety and operational competence, making it relevant for press brake operators aiming to enhance their operational skills.
The National Institute for Metalworking Skills (NIMS) and the Fabricators & Manufacturers Association, International (FMA) offer certifications that are widely recognized in the metalworking industry. These certifications cover a range of skills, including press brake operation, and ensure that operators meet high industry standards. The FMA Precision Press Brake Certificate, in particular, focuses on precision and advanced techniques in press brake operation, including machine setup, programming, and quality control.
A high school diploma or GED is essential, but additional training through apprenticeships or technical schools is highly beneficial. These programs provide foundational knowledge and practical skills essential for press brake operation.
To excel as a press brake operator, several key skills and qualities are necessary. Technical proficiency is crucial for understanding machinery and its maintenance. Attention to detail ensures all aspects of the job meet strict standards, while mathematical skills are needed for precise measurements and adjustments. Physical stamina and strength are required to manage the job’s physical demands. Additionally, problem-solving abilities help in identifying issues and determining effective solutions, and a safety-oriented mindset is critical for maintaining a safe work environment and adhering to safety guidelines.
Certifications offer numerous advantages for press brake operators:
By obtaining relevant certifications and qualifications, press brake operators can advance their careers, improve their skills, and contribute to higher standards of safety and quality in the industry.
Ensuring the safety of press brake operators involves adhering to a comprehensive set of protocols designed to minimize risks and prevent accidents. These protocols cover various aspects of operation, from initial training to daily practices.
Safety devices are critical components that help protect operators from injuries during press brake operations.
Operators must wear appropriate PPE to protect themselves from potential hazards.
Adherence to safety standards is essential to ensure a safe working environment.
Understanding common hazards and implementing measures to mitigate them is crucial for operator safety.
By integrating these safety protocols, devices, and practices into the training curriculum, press brake operators can significantly reduce the risk of accidents and create a safer working environment. Regular training sessions and adherence to safety standards are key components of a comprehensive safety strategy.
Proper maintenance of press brakes is crucial for ensuring their longevity and optimal performance. Regular maintenance routines help prevent unexpected breakdowns and maintain safety standards.
Effective troubleshooting techniques are essential for addressing issues promptly and maintaining the efficiency of press brake operations.
By adhering to these maintenance and troubleshooting practices, press brake operators can ensure the efficient, safe, and reliable operation of their equipment. Regular maintenance and prompt troubleshooting not only enhance machine performance but also extend its lifespan.
A notable case study by Midwest Engineering Systems showcases the benefits of integrating robotic systems into press brake operations. The implementation of an ABB Robot System, which includes automatic tooling changes and part handling systems, significantly increased productivity and improved worker safety by reducing direct human interaction with the press brake. This automation also enhanced the quality of finished parts. The system met ANSI/RIA safety standards, underscoring the importance of adhering to safety regulations while adopting new technologies.
Effective training programs are crucial for developing skilled press brake operators. Training programs should offer both theoretical knowledge and practical experience. Classroom and online training options provide flexibility, while hands-on training is essential for building muscle memory and confidence in operating the machinery. Key training components should cover setup, tooling selection, bending operations, safety protocols, and maintenance procedures.
Regular performance evaluations help ensure that operators maintain high standards of safety and efficiency. Employers should conduct practical and written tests to gauge operators’ understanding of operational procedures and safety standards. Periodic refresher training sessions reinforce safe practices and update operators on new safety protocols and technology. Immediate feedback from supervisors can address any performance issues and promote continuous improvement.
Adhering to safety protocols is paramount in press brake operations. Operators should use safety devices such as two-hand tripping devices, emergency stop buttons, safety interlocks, and light curtains. These measures help minimize the risk of injury. Personal protective equipment, such as safety glasses, gloves, and appropriate clothing, is essential. Ensuring that safety devices are functional and properly maintained is a critical component of daily operations.
Regular maintenance is vital for the optimal functioning of press brakes. Daily tasks include cleaning, inspecting for wear or damage, and ensuring all safety guards are operational. Hydraulic and electrical system maintenance should be performed periodically, including monitoring fluid levels, replacing filters, and checking wiring and safety circuits. Effective troubleshooting techniques, such as adjusting hydraulic pressure and inspecting electrical connections, help address issues promptly and maintain machine efficiency.
New press brake operators should be supervised until they demonstrate proficiency in operating the machinery safely. Providing immediate feedback and support helps new operators develop confidence and competence. It’s essential to ensure materials are clean, flat, and correctly positioned on the bed for accurate bending. Choosing the correct punch and die sizes based on material thickness and bending requirements is another critical aspect of training new operators.
By integrating these best practices, manufacturers can ensure that their press brake operators are well-trained, productive, and safe in their roles. Continuous training, adherence to safety protocols, and regular maintenance are key factors in achieving high standards of efficiency and safety in press brake operations.
Below are answers to some frequently asked questions:
The best training programs for press brake operators include vocational schools, technical colleges, and apprenticeships, which provide a mix of theoretical and practical knowledge. Programs like the Precision Press Brake Certificate offered by FMAMFG and the MC Machinery training courses (Level 1 and Level 2) are highly recommended. These programs cover essential topics such as machine operation, safety protocols, programming, tooling, and maintenance, ensuring operators gain comprehensive skills and industry-recognized certifications. It’s crucial to choose a program that matches the specific needs of the operator and offers a balance of hands-on experience and theoretical learning.
Press brake operators should follow stringent safety protocols to ensure a secure working environment. These include performing pre-operation checks, utilizing safeguarding devices like light curtains and interlocks, and avoiding placing hands near the dies. Operators must wear appropriate PPE, such as gloves and safety helmets, and be familiar with emergency stop buttons. Regular maintenance and basic troubleshooting are essential for machine upkeep. Comprehensive training and adherence to safety standards, like OSHA and ANSI, are crucial. Keeping the work area clean and orderly further reduces risks and enhances operational efficiency.
Valuable certifications for press brake operators include the NIMS certification, the FMA Precision Press Brake Certificate, and the Press Brake Safeguarding Certificate. These certifications validate an operator’s skills, enhance their safety compliance, and improve career prospects. They cover essential topics such as precision sheet metal vocabulary, mathematical concepts, blueprint interpretation, machine safeguarding standards, and safety protocols. Additionally, certifications like the Forklift Safety and Inspector Certification, Certified Welding Engineer (CWEng), and Operator Certification further complement an operator’s qualifications in metal fabrication and equipment safety.
To maintain and troubleshoot a press brake effectively, follow a comprehensive maintenance schedule and address common issues promptly. Daily tasks include cleaning the machine and inspecting for loose or damaged parts. Weekly, lubricate moving parts and check hydraulic hoses for leaks. Periodically, verify and change hydraulic oil and filters. For troubleshooting, address hydraulic leaks, pressure issues, and ram movement problems by inspecting seals, connections, and system settings. Resolve operational issues like uneven bending and excessive noise by ensuring proper alignment and replacing worn components. Regular training and adherence to safety protocols, as discussed earlier, are crucial for optimal performance and safety.
To become a proficient press brake operator, essential skills include basic mechanical knowledge for troubleshooting and machine operation, proficiency in math and measuring for precise fabrication, and the ability to read blueprints. Safety awareness is crucial, requiring adherence to strict safety protocols and use of personal protective equipment. Operators should also be skilled in computer operation for programming CNC machines. Effective communication, teamwork, problem-solving abilities, and adaptability to new tools and procedures are important soft skills. Physical stamina and strength are necessary for handling materials and standing for long periods, ensuring successful operation and maintenance of press brake machines.