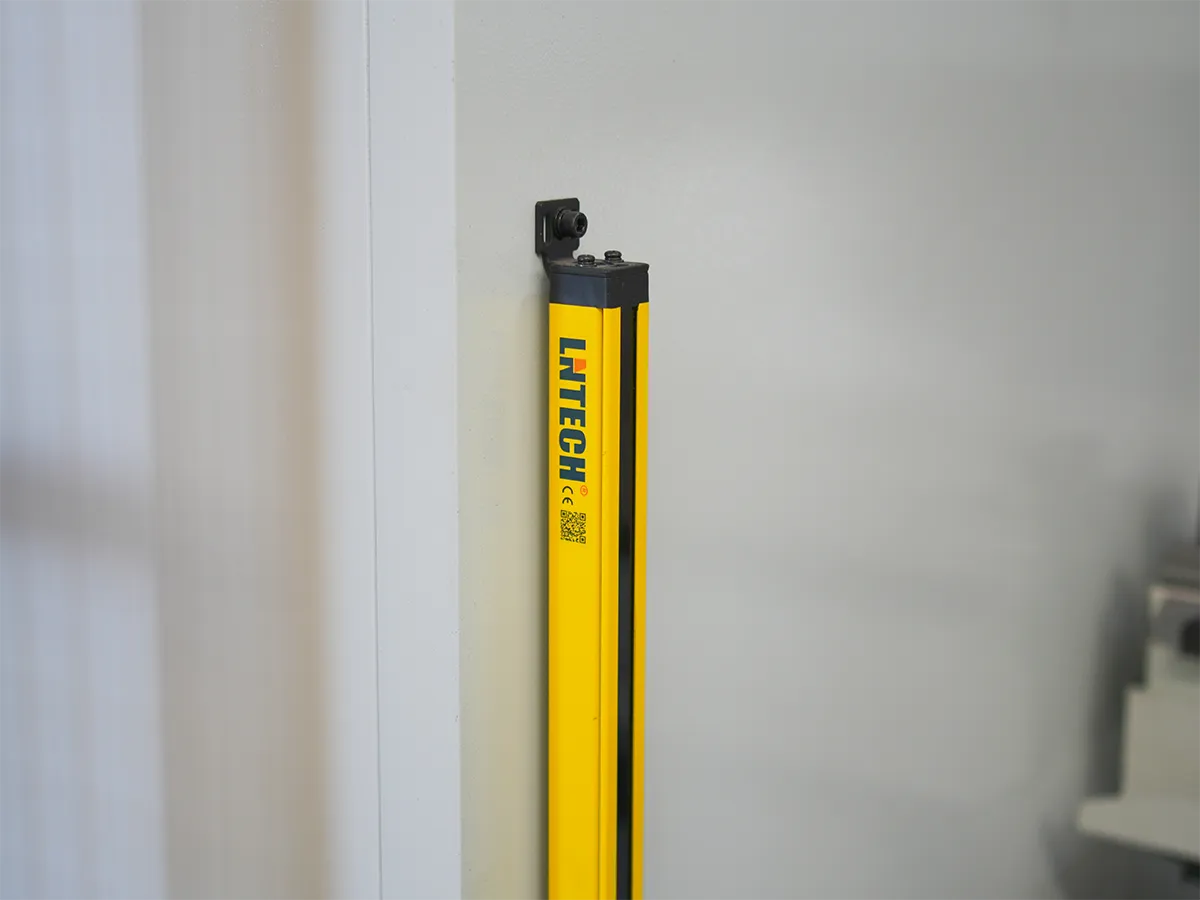
In the world of metal fabrication, the choice between hydraulic and electric press brakes can make a significant impact on efficiency, precision, and overall production costs. Whether you’re an engineer seeking the highest precision for intricate bends or a manufacturing manager aiming to reduce energy consumption, understanding the nuances of these two types of press brakes is crucial. This article delves into the key differences, examining everything from energy efficiency and operating costs to precision, speed, and maintenance requirements. Ready to discover which press brake aligns best with your production needs and industry standards? Let’s dive in and explore the intricacies of hydraulic versus electric press brakes.
Press brakes are vital machines in metal fabrication, used to bend and shape sheet metal with precision and consistency.
A typical press brake consists of a sturdy frame, a table, a movable upper beam, and a set of tools (punch and die). The workpiece is placed on the table, and the upper beam, driven by various mechanisms depending on the type of press brake, moves downward to press the metal into the desired shape.
Press brakes come in various types, including mechanical, CNC, and pneumatic. Mechanical press brakes use a flywheel driven by an electric motor for fast and consistent bends. CNC press brakes offer high precision and repeatability through computer control, ideal for complex tasks. Pneumatic press brakes use compressed air and are suitable for lighter-duty applications.
Press brakes are versatile machines used in industries such as automotive, aerospace, and construction. They create components like car brackets, aircraft panels, and building frames from materials like steel, aluminum, and copper.
Operating press brakes requires adherence to safety protocols to prevent accidents and injuries. Modern press brakes are equipped with safety features such as light curtains, emergency stop buttons, and protective guards to ensure operator safety.
In summary, press brakes are essential in metal fabrication for their precision, versatility, and efficiency. Understanding their types, components, and applications is crucial for anyone in the industry, ensuring high-quality and consistent manufacturing results.
There are several types of press brakes, each with unique features and benefits. Here’s a closer look at each type:
Mechanical press brakes use a flywheel driven by an electric motor to store kinetic energy, which is then transferred to the ram via a clutch mechanism. These machines are fast and consistent, making them ideal for high-volume production. They handle a variety of materials with relatively straightforward adjustments.
CNC (Computer Numerical Control) press brakes use computer control to manage the movement of the ram and the positioning of the back gauge. This ensures high accuracy and repeatability. These machines are perfect for complex bending tasks and can store numerous programs for different jobs. This significantly reduces setup time and increases productivity, making them essential in environments where precision and efficiency are paramount.
Pneumatic press brakes operate using compressed air to drive the ram. They are generally used for lighter-duty applications where high force is not required. These machines are simpler in design and maintenance compared to hydraulic and electric press brakes. Pneumatic press brakes are suitable for applications involving thin materials and are often chosen for their lower operational costs and ease of use.
Hydraulic press brakes generate significant force, making them ideal for heavy-duty applications. They use hydraulic fluid pressure to move the ram and can handle a wide range of materials and thicknesses. These machines offer smooth and consistent bending operations and are capable of handling large production volumes. Modern hydraulic press brakes often come with advanced features such as programmable controls and automatic tool changes, enhancing their efficiency and usability.
Electric press brakes use servo motors and ball screws to drive the ram with high precision. They are energy-efficient, consuming power only during the bending process. These machines are also quieter and require less maintenance compared to hydraulic press brakes. Electric press brakes are well-suited for applications requiring high precision and repeatability, making them an attractive option for many manufacturing environments.
Hybrid press brakes combine the benefits of both hydraulic and electric systems. They use a combination of hydraulic cylinders and electric servo motors to drive the ram. This configuration provides the high force capacity of hydraulic systems with the precision and energy efficiency of electric systems. Hybrid press brakes are designed to offer the best of both worlds, making them suitable for a wide range of applications, from heavy-duty tasks to high-precision operations.
Electric press brakes are highly energy-efficient, consuming power only during active bending, which significantly lowers operating costs. This efficiency is due to the use of servo motors that draw power on-demand, unlike hydraulic systems that maintain constant pressure and consume energy even when idle.
In contrast, hydraulic press brakes use continuously running pumps to maintain system pressure. This continuous operation leads to higher energy consumption, making them less efficient compared to their electric counterparts. Although advancements in hydraulic technology have led to more energy-efficient models, they generally consume more power than electric press brakes.
Electric press brakes offer precision up to 0.000079 inches (1 micron), ideal for applications demanding high standards and repeatability. They use advanced servo motors and ball screws, allowing for highly accurate positioning and faster cycle times. This makes them suitable for tasks requiring exacting standards and high repeatability.
Hydraulic press brakes also provide high precision, though not to the same degree as electric models, typically reaching up to 0.0004 inches (10.16 microns). While they may be slightly slower, they are still capable of performing complex and precise bending tasks, making them suitable for a wide range of applications.
Hydraulic press brakes are renowned for generating significant bending forces, making them ideal for handling thicker materials and heavy-duty applications. They can exert higher tonnage, allowing them to bend thicker and tougher materials that electric press brakes might struggle with.
Electric press brakes, while precise and efficient, are generally better suited for lighter applications. They are typically used for small to medium production runs and are most effective with thinner materials. For operations that do not require extremely high bending forces, electric press brakes provide a balance of precision, speed, and efficiency.
Electric press brakes require less maintenance than hydraulic ones because they lack hydraulic components, resulting in fewer parts that need servicing. This leads to lower maintenance costs and reduced downtime, making electric press brakes a cost-effective option in the long run.
Hydraulic press brakes, however, need regular maintenance to ensure optimal performance. This includes checking and replacing hydraulic fluid, inspecting seals and hoses for leaks, and maintaining the hydraulic pump. While this maintenance can be more labor-intensive and costly, it is essential to keep the machine running smoothly and prevent potential breakdowns.
Hydraulic press brakes are versatile and ideal for large-scale production and complex metal forming tasks. They are commonly used in industries such as automotive, aerospace, and construction, where the ability to handle thick materials and produce precise bends is crucial.
Electric press brakes are best suited for small to medium production runs where high precision and speed are critical. They are ideal for applications involving thinner materials and requiring frequent setup changes. Their energy efficiency and lower maintenance needs also make them attractive for manufacturers looking to reduce operational costs while maintaining high-quality output.
Both hydraulic and electric press brakes come equipped with advanced safety features to protect operators. Hydraulic press brakes often include emergency stop buttons, light curtains, and foot-operated controls to minimize the risk of accidents. These features are designed to enhance operator safety by preventing sudden movements and ensuring controlled operation.
Electric press brakes also incorporate similar safety features, including light curtains and emergency stops. Additionally, the precise control offered by electric systems can contribute to safer operation by reducing the likelihood of unexpected movements.
Hydraulic press brakes are designed for durability and long service life. The hydraulic system helps reduce wear and tear on mechanical components, which can extend the lifespan of both the machine and its tooling. Regular maintenance is crucial to ensure this longevity, but with proper care, hydraulic press brakes can provide reliable performance for many years.
Electric press brakes, while also durable, benefit from having fewer mechanical components that can wear out. This can result in a longer lifespan with less frequent maintenance. The precision and efficiency of electric press brakes make them a valuable investment for operations focused on high-quality production with minimal downtime.
Electric press brakes are highly energy-efficient, using power only during the bending process with on-demand servo motors. When idle, these machines do not consume power, leading to substantial energy savings over time. This on-demand power consumption reduces energy costs and minimizes environmental impact, making electric press brakes an eco-friendly option for manufacturers.
In contrast, hydraulic press brakes are less energy-efficient because their hydraulic pumps and motors run continuously, even when not in use. Although hydraulic press brakes can deliver the same tonnage with potentially lower initial electrical energy consumption, their continuous operation results in higher overall energy usage compared to electric press brakes.
The energy efficiency of electric press brakes translates directly into lower operating costs. Reduced energy consumption means lower utility bills, which is particularly advantageous in regions with high electricity prices. Additionally, the precise control of electric press brakes minimizes material waste, further contributing to cost savings. Over time, these factors can make electric press brakes a more cost-effective choice for manufacturers looking to optimize their operational expenses.
Hydraulic press brakes incur higher operating costs primarily due to their increased energy consumption. The continuous power required to operate hydraulic components, such as pumps and motors, leads to higher utility bills. While hydraulic press brakes may have lower initial energy consumption to deliver the same tonnage, the ongoing operation costs are typically higher due to the constant energy draw.
Electric press brakes need less maintenance than hydraulic ones, as they lack hydraulic components that require regular servicing. This reduction in maintenance requirements not only lowers maintenance costs but also minimizes machine downtime, enhancing overall productivity.
Hydraulic press brakes necessitate regular maintenance to ensure optimal performance. This includes routine checks and replacements of hydraulic fluid, seals, and other components. The ongoing maintenance needs can add to the overall operational costs, making hydraulic press brakes more labor-intensive and costly to maintain compared to their electric counterparts.
Hydraulic press brakes cost between $30,000 and $200,000, depending on features. Although electric press brakes may have a higher initial cost, they offer long-term savings on energy and maintenance.
Electric press brakes, particularly servo-driven models, offer significant long-term savings. For example, a servo press brake can reduce power consumption by up to 62% compared to conventional hydraulic press brakes. These substantial savings in electricity costs can potentially recover the extra cost of the machine within a few years of purchase, making electric press brakes a financially prudent investment for many manufacturers.
In summary, hydraulic press brakes are best for heavy-duty tasks, but electric press brakes are more energy-efficient and cost-effective for many manufacturers.
Electric press brakes are renowned for their exceptional precision, often achieving accuracies up to 0.000079 inches (2 microns), thanks to advanced motor systems and precise control mechanisms. These machines are designed to provide consistent and repeatable motion, which is crucial for applications demanding high precision and consistency in bends. In contrast, hydraulic press brakes typically offer slightly lower accuracy, around 0.0004 inches (10 microns), influenced by factors such as oil temperature and pressure fluctuations.
When it comes to speed, electric press brakes excel with faster cycle times. The advanced motor systems provide rapid acceleration and deceleration, reducing overall cycle time. This makes electric press brakes ideal for small to medium production runs where quick setup changes and fast cycle times are crucial. On the other hand, hydraulic press brakes, while powerful and capable of handling heavy-duty applications, generally have slower cycle times due to the time required to build and release hydraulic pressure.
Electric press brakes are more energy-efficient because they only use power during the bending process. This on-demand power consumption reduces energy costs and minimizes environmental impact. In contrast, hydraulic press brakes require continuous operation of hydraulic pumps, leading to higher energy consumption.
Electric press brakes also offer operational efficiency with features like variable speed drives and regenerative braking systems that capture and reuse energy. These systems optimize energy use, reduce waste, and minimize heat generation, extending the machine’s lifespan and reducing maintenance costs.
Electric press brakes require less maintenance due to fewer moving parts and the absence of hydraulic fluids. This reduces the frequency and cost of maintenance, minimizing downtime and prolonging the machine’s lifespan. Hydraulic press brakes, however, need regular maintenance to ensure optimal performance, including checking and replacing hydraulic fluid, inspecting seals, and maintaining the hydraulic pump.
Electric press brakes are more flexible and suitable for environments requiring frequent die changes or setups. They offer faster setup times and the ability to store and recall multiple bending programs through CNC controls, enhancing their efficiency and flexibility. This makes them ideal for production environments that demand quick changes and high adaptability.
Electric Press Brakes:
High precision (up to 0.000079 inches)
Faster cycle times
Energy-efficient (power used only during bending)
Less maintenance required
Flexible and quick setup times
Hydraulic Press Brakes:
Strong bending force
Suitable for heavy-duty applications
Slightly lower precision (around 0.0004 inches)
Higher energy consumption due to continuous operation
Robust power for large-scale production
In summary, electric press brakes offer unmatched precision and speed, making them perfect for industries requiring quick turnarounds and high accuracy. Meanwhile, hydraulic press brakes, with their robust power, are ideal for heavy-duty applications despite their slightly slower cycle times.
Hydraulic press brakes are renowned for their powerful force capabilities, making them ideal for heavy-duty applications. These machines utilize hydraulic fluid pressure to generate significant bending forces, which can range from a few tons to several thousand tons. This immense force capacity allows hydraulic press brakes to handle thick and tough materials, such as steel and aluminum, efficiently.
Hydraulic press brakes are particularly advantageous for large-scale production environments where high force and capacity are essential. They can bend thicker materials with ease, ensuring consistent and reliable performance even under demanding conditions. This makes them ideal for industries such as automotive, aerospace, and construction, where precision and durability are critical.
Electric press brakes are designed for applications requiring precision and efficiency rather than raw force. These machines use servo motors and ball screws to drive the ram, providing highly accurate and repeatable bending motions, although they may not match the force capacity of hydraulic press brakes.
Electric press brakes are usually used for lighter tasks and smaller production runs. Their force capacity is generally lower, making them more suitable for bending thinner materials. However, the precision and control offered by electric press brakes make them an excellent choice for industries where exacting standards and repeatability are paramount.
Hydraulic press brakes are the preferred choice for heavy-duty operations because of their high force and capacity. They are capable of handling large-scale production runs and bending thick materials with ease. This makes them indispensable in industries that require robust and reliable performance.
Electric press brakes are better suited for tasks that require high precision and intricate detailing. Their advanced servo motor systems and precise control mechanisms make them ideal for small to medium production runs where accuracy and repeatability are crucial. Industries such as electronics, medical devices, and precision metalworking benefit significantly from the capabilities of electric press brakes.
In conclusion, the choice between hydraulic and electric press brakes depends on the specific needs of your production process, with hydraulic press brakes offering higher force and capacity for heavy-duty applications and electric press brakes excelling in precision, speed, and energy efficiency for smaller, high-precision tasks. Understanding the force and capacity requirements of your application is essential in selecting the right press brake for your needs.
Hydraulic press brakes need regular, extensive maintenance due to their complex systems. Regular maintenance tasks for hydraulic press brakes include checking and changing hydraulic fluid, replacing filters, inspecting seals, maintaining pumps, and conducting comprehensive system inspections. These activities are essential for preventing downtime and ensuring the longevity and reliability of hydraulic press brakes.
Electric press brakes require less maintenance compared to their hydraulic counterparts. Key maintenance tasks include regularly inspecting electrical components like servo motors and control systems to ensure proper function, keeping the control software up-to-date, checking mechanical parts like ball screws and linear guides, and maintaining the cooling systems for electrical components to prevent overheating. Overall, the maintenance for electric press brakes is simpler and less frequent, contributing to lower maintenance costs and reduced downtime.
Maintenance costs for hydraulic press brakes can be high due to the complexity of their systems. These costs include hydraulic fluid replacement, filter and seal costs, labor costs, and the impact of downtime. Frequent maintenance can lead to more downtime, impacting production schedules and efficiency.
Electric press brakes have lower maintenance costs due to fewer moving parts and the absence of hydraulic components. Cost considerations include servicing electrical components, keeping software updated, and enjoying reduced downtime. Less frequent maintenance leads to enhanced productivity and cost-efficiency.
In summary, hydraulic press brakes are powerful but require more maintenance and higher costs. Electric press brakes, with fewer maintenance needs and lower costs, offer a more cost-effective solution for many manufacturers.
Hydraulic press brakes are ideal for large-scale and heavy-duty tasks because they can generate significantly higher bending forces. These machines can handle thicker materials, often exceeding 20 mm in thickness. Industries such as shipbuilding, large-scale construction, and heavy metal fabrication benefit from the robust capabilities of hydraulic press brakes. Their high force capacity ensures that even the most demanding bending tasks can be completed efficiently and reliably.
Electric press brakes excel in small to medium production runs and precise bending tasks due to their high precision and repeatability. These machines are suitable for industries like aerospace and medical device manufacturing. The ability to program electric press brakes for automatic bending sequences enhances their utility in automated production environments. This programmability reduces setup times and increases flexibility, making electric press brakes a versatile choice for various manufacturing needs.
In aerospace, precision and consistency are crucial, making electric press brakes the preferred choice. The aerospace sector often deals with thin, high-strength materials that require exacting standards, making electric press brakes the ideal choice.
The automotive industry benefits from both hydraulic and electric press brakes. Hydraulic press brakes are used for forming thicker metal parts, such as chassis components, due to their high force capabilities. Electric press brakes are utilized for precision tasks, such as bending thinner sheet metal parts used in car bodies and interior components.
The construction industry relies heavily on hydraulic press brakes for their ability to handle large and thick materials. These machines are essential for fabricating structural components, such as beams and columns, which require significant bending force. Hydraulic press brakes ensure that these critical parts are manufactured with the necessary strength and accuracy.
Electric press brakes are ideal for medical device manufacturing due to their precision and cleaner operation, as they don’t use hydraulic fluids. The ability to achieve tight tolerances and repeatable results is crucial for producing medical devices that meet stringent regulatory standards.
Shipbuilding involves the fabrication of large, thick metal plates and components. Hydraulic press brakes are indispensable in this industry because of their capacity to generate high bending forces. These machines ensure that the large-scale metal parts used in ship construction are formed accurately and efficiently, contributing to the overall integrity and safety of the vessels.
Hydraulic press brakes can pose environmental risks from potential hydraulic fluid leaks, which can contaminate soil and water. This makes them less suitable for environmentally sensitive applications. Electric press brakes, with their cleaner operation, are a better choice for industries prioritizing environmental sustainability.
Hydraulic press brakes typically require more space for operation and material handling, which can be a challenge for smaller workshops. They also generate more noise due to the continuous operation of hydraulic pumps. Electric press brakes, being quieter and more compact, are better suited for noise-sensitive environments and smaller manufacturing spaces.
The choice between hydraulic and electric press brakes depends on the specific requirements of the production environment. Hydraulic press brakes are best for heavy-duty, large-scale applications requiring high bending forces, while electric press brakes are ideal for precise, automated, and energy-efficient bending tasks.
Choosing between hydraulic and electric press brakes? Consider factors like energy efficiency, precision, force capacity, maintenance, and application suitability.
Electric press brakes are more energy-efficient since they use power only during bending. This reduces operating costs and environmental impact. Hydraulic press brakes, however, run continuously, consuming more energy and incurring higher costs.
Electric press brakes deliver higher precision and faster cycles thanks to advanced servo motors, perfect for high-accuracy tasks. Hydraulic press brakes, though slightly less precise, offer strong power and stability for standard precision jobs.
Hydraulic press brakes are best for high-force tasks and thick materials, making them great for heavy-duty use. Electric press brakes are ideal for lighter tasks with thinner materials, usually up to 10-15 mm thick.
Electric press brakes need less maintenance and have fewer parts, leading to less downtime and lower costs. Hydraulic press brakes require regular checks on fluids and seals, resulting in more downtime and higher maintenance costs.
The choice between hydraulic and electric press brakes should be guided by the specific requirements of your manufacturing operations. Consider factors such as the type of materials you will be working with, the precision needed, production volume, and long-term operational costs. By carefully evaluating these aspects, you can select the press brake that best meets your production needs and enhances your overall efficiency and productivity.
Below are answers to some frequently asked questions:
The key differences between hydraulic and electric press brakes lie in their power consumption, precision, force capacity, maintenance needs, and application suitability. Electric press brakes are more energy-efficient, consuming power only during the bending process, and offer higher precision and speed, ideal for small to medium production runs. In contrast, hydraulic press brakes provide greater force and stability, making them suitable for heavy-duty applications and thicker materials, though they require more maintenance due to the complexity of their hydraulic systems. The choice between the two depends on specific operational needs, including required force, precision, and production volume.
Electric press brakes are more energy-efficient than hydraulic press brakes. They consume energy only during the bending operation and shut off during idle periods, significantly reducing overall energy consumption. In contrast, hydraulic press brakes run their motors and pumps continuously, even when idle. Additionally, electric press brakes incorporate advanced energy-saving technologies like variable speed drives and regenerative braking systems, further optimizing energy use. This efficiency results in lower operating costs and a smaller environmental impact, making electric press brakes a more sustainable and cost-effective option for manufacturers.
Electric press brakes offer higher precision and faster cycle times compared to hydraulic press brakes. Electric models can achieve an accuracy of up to 0.000079 inches (1 micron) and have quicker descent and return speeds, making them ideal for applications requiring high accuracy and rapid bending operations. In contrast, hydraulic press brakes, while powerful and suitable for heavy-duty tasks, typically have an accuracy of 0.0004 inches (10.16 microns) and are slightly slower due to the hydraulic system’s operation. Thus, for tasks demanding precision and speed, electric press brakes are the preferred choice.
Hydraulic press brakes require regular inspections for fluid leaks, hose wear, and lubrication, as well as periodic hydraulic fluid and filter changes. They also need component cleaning, calibration, and alignment checks. Electric press brakes, on the other hand, have reduced maintenance needs, primarily involving servo motor upkeep and electronic component checks, eliminating the need for fluid maintenance. Both types benefit from routine cleaning, lubrication, and regular operational checks to ensure reliability, safety, and cost savings through preventive maintenance, as discussed earlier.
Hydraulic press brakes are suitable for heavy-duty applications due to their ability to generate significantly higher bending forces, making them ideal for handling thicker and heavier materials. They provide continuous and stable power output, ensuring high stability and precision for extended periods of operation. Additionally, hydraulic press brakes are versatile and adaptable to various materials and tasks, making them well-suited for industries such as construction, shipbuilding, and heavy machinery manufacturing. Despite requiring more maintenance, their robust performance and durability make them the preferred choice for demanding, large-scale production environments.